
图为12月15日,三门核电一号CV底封头在运输途中
09年12月21日15时28分,我国第三代核电自主化依托项目首台机组、世界上首台第三代核电AP1000机组——三门核电站一号机组核岛钢制安全壳底封头成功实现整体吊装就位。这是我国积极探索以“标准化设计、工厂化预制、模块化建造、专业化管理、自主化建设”为主要特征的第三代核电自主化发展新路子所取得的又一项新突破。

当日中午12时08分,三门核电站一号机组核岛钢制安全壳底封头开始从运输车上徐徐吊起,与吊梁分配器连接的8根吊索受力均匀。此后,通过转杆、变幅、回钩等吊装操作,钢制安全壳底封头准确就位于1号机组核岛底座上。整个吊装过程历时三小时零八分。
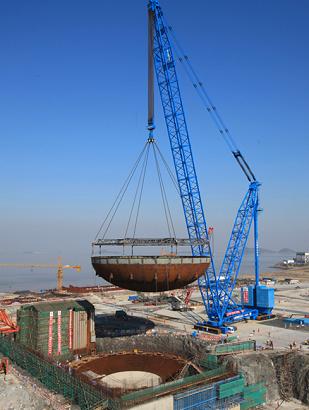
国家核电技术公司党组书记、董事长王炳华表示,三代核电AP1000依托项目首套钢制安全壳底封头的整体吊装就位,是世界先进核电建设的一项壮举,是我国在先进核电装备制造领域取得的新突破。我国高起点引进三代先进核电技术,对提升装备制造业整体能力的带动作用已经显现出来。
吊装就位的三门核电站一号机组核岛钢制安全壳底封头直径近40米,钢板厚约42毫米,整体起吊重量达950吨(其中,底封头自重660吨),其工厂制造和现场组焊质量完全满足第三代核电AP1000设计规范的要求。
王炳华介绍,三门核电站一号机组核岛钢制安全壳底封头的钢材制造、弧形钢板压制、现场拼装焊接、焊接材料生产、整体运输吊装等都是由中国企业自主承担完成的。中方企业攻克了诸多世界性的技术难题和工艺难关,使我国成为在世界上率先掌握这项新技术的国家,较大地提升了我国核电装备制造和相关材料研制的水平。这是为世界核电同行高度关注、令国内业界人士引以为豪的事情。
第三代核电AP1000是目前世界上最安全、最先进的核电技术,采用了革新性的非能动安全设计理念,在世界上首次采用在核电站反应堆压力容器外增加钢制安全壳的新技术。三门核电站工程建设的顺利推进,对于我国先进核电技术的自主化发展具有重要的示范作用。
世界首套三代核电钢制安全壳底封头的钢材由宝钢集团公司制造,拼装组成底封头的四层64张弧形钢板由“国家核电”山东核电设备制造有限公司压制,底封头主焊缝的焊接任务由中国核工业第五建设公司AP1000施工总承包部承担完成,焊材由上海大西洋公司自主研制完成,吊装实施由中国核工业中原建设公司承担完成。
在三门核电站一号机组核岛钢制安全壳底封头的钢材制造、弧形钢板压制、现场拼装焊接、焊接材料生产、整体运输吊装过程中,“国家核电”三门核电现场管理机构(SPMO)与项目业主三门核电有限公司、施工方中国核工业第五建设公司等单位协同合作,有序推进了底封头制造、吊装就位的各项准备工作,保证了安全和质量控制。
山东核电设备制造有限公司的技术专家介绍,钢制安全壳是第三代核电AP1000核岛最为重要的关键设备之一,为圆柱形容器,由中间的圆柱形筒体及上下两个椭圆型封头组成(下面的椭圆型封头称“底封头”,上面的椭圆型封头称“上封头”)。钢制安全壳最大直径39.624米,总高度65.633米,体积约70000立方米,总重量约3600吨。钢制安全壳(CV)底封头单张钢板的规格约为10米×4米×44毫米,其典型特征是大尺寸、多曲率、高精度,采用整体模压一次成型技术,当前该技术尚属世界性难题。
第三代核电AP1000的反应堆压力容器、蒸汽发生器等核心设备,以及相关的结构模块均安装在钢制安全壳内。钢制安全壳底封头的顺利吊装就位,将拉开三门核电站一号机组核岛(核反应堆)厂房步入建造高峰的帷幕。
【责任编辑:${content.getAttrByFlatName('zrbj').value}】