航天科技五院以信息化科学提升项目质量
航天科技五院以信息化科学提升项目质量
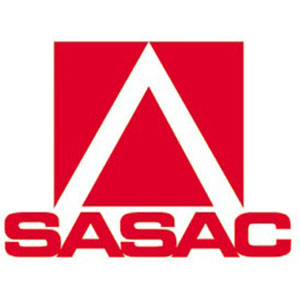
着眼于型号任务复杂程度、工程管理难度日益增加给保成功带来的严峻挑战,中国航天科技集团公司五院以“宇航智造”工程为抓手,通过基于模型的数字化协同研制平台建设,积极牵引、推动产业模式转型升级,用效率、效益的跃升更为科学地保成功。
通过半年多的持续努力,以基于模型数字化协同研制平台建设为代表的信息化项目取得重要进展,在缩短研制周期、优化生产流程、提升产品质量方面收获了不少成果。
提升生产整体效能
“消除短板才能最大程度提升整体能力”,年初,五院在部署信息化工作时就认识到,推进信息化与产业化的深度融合是一项系统工程。
对此,五院聚焦型号任务设计、研制、试验、产保等全周期工作,从数字化设计与仿真验证、制造集成、数字化测试试验、信息化全生命周期管理等方面发力,提升宇航产业生产整体效能。
在数字化设计与仿真验证方面,该院成立了基于模型的系统工程技术研究与应用工作组,以实践十九号、东方红五号卫星平台等为试点,进行了系统设计与仿真的工程实践。
通过深入推进总体与载荷、控制协同设计,在明确内容和流程的基础上,五院不断完善协同设计的平台与系统,并在高分系列卫星上应用成功。
该院还深入推进航天器信息流一体化设计,开发了航天器电子信息接口数据管理系统,在遥感、硬X射线调制望远镜卫星等型号中大显身手,将以往1至2个月的测试准备时间大幅缩短为1到2天。
在推进航天器供配电专业的数字化设计方面,五院通过应用供配电大图软件,将单星供配电系统的设计周期缩短了近九成,并将空间站供配电电缆设计周期缩短了50%以上。
从源头根除“信息孤岛”
在制造集成方面,五院深入推进三维工艺、MES等系统建设应用,组织所属单位结合自身实际,开展了诸多“本地化”探索,完成了部装现场“工艺-模型-实物”可视化互动系统的开发,有力支撑了部装工艺设计由二维向三维转变这一颠覆性跨越。
通过建立工艺数字样机快速构建及轻量化模型综合查询系统,五院实现了总装设计模型信息的自动提取与现场工艺信息的分类整合与推送,有效提升了AIT现场操作效率。
另外,该院还完成了三维工艺系统与MES系统集成和可视化表格的二次开发,实现了车间快速排产和可视化加工。截至目前,五院型号任务AIT工作已经基本实现了三维工艺现场可视化支持,总装人员的操作模式全面步入“量化、精准化”的新时代。
在数字化测试试验方面,五院进一步推进航天器一体化测试系统完善与应用,促进系统向智能化方向发展;完成了磁试验数据采集软件开发,实现了磁场调节、整星及部组件磁场数据采集,零磁场和地磁场下的磁矩计算,以航天“云试验”建设方案为代表的新实验模式正在快马加鞭开展论证。
在科研生产管理方面,该院通过深入推进院所两级科研生产管理系统完善与应用,完成了科研生产综合管理系统中“两重一共”问题管理功能、待办事项管理功能、产品发布系统的开发;围绕多型号项目管理需求,深入开展了新一代项目管理系统的建设论证。
此外,为从源头上根除各单位在推动信息化建设中各自为战所引发的“信息孤岛”、信息流“断头路”问题,五院从顶层着手,正式发布了《五院宇航产品数字化研制工程软件管理办法》,完成了9项标准规范的立项论证,进一步统一了各领域、接口间的标准规范,为信息流在产业链各环节、各型号间的畅游奠定了基础。
后续,五院将通立项实施“航天器发射场远程支持”项目、建设整星AIT状态管理系统、编制发布十余个院级数字化标准规范等措施,继续把信息化建设进行到底,全面提升质量,科学备战确保后续任务圆满成功。