电弧增材制造技术 航天科工勇当军工行业拓荒者
电弧增材制造技术 航天科工勇当军工行业拓荒者
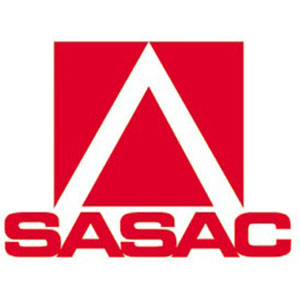
力学性能提升15%,单件研制周期从1个月缩短至15小时,材料利用率由70%提升至90%,这可以说是某预研型号舱段制造技术从铸造变为电弧增材制造带来的飞跃。
中国航天科工三院239厂勇当电弧增材制造技术在军工行业的拓荒者,历经2年时间,发展效果显著。
需求牵引,军工行业首个平台落地239厂
航空航天技术是国防实力的象征,世界各国都试图以更快的速度研发出更新的武器装备,使自己在国防领域处于不败之地。然而,型号研制阶段的模型变化常有发生,传统工艺技术难以满足“快速研制”的需求,厂技术人员时刻找寻着一种能实现“快速研制”的新技术。
在一次去高校的技术调研和交流中,厂技术人员收获满满。他们了解到一项“新”技术,该技术省去了传统制造技术成形过程中的模具设计、模具制造、反复修模等流程,实现了从三维模型到产品毛坯的直接快速制造,它就是电弧增材制造技术,从传统的弧焊发展而来,用电弧热将丝材熔化并按预定轨迹逐层堆积成金属结构件,有着研制周期短、沉积效率高、设备成本及运行成本低、材料利用率高等特点。
“这项高效低成本的“新”技术十分符合总装厂大型高性能金属结构件的快速研制生产需求,也符合239厂“差异化、核心化、优势化、高端化”的技术发展方向,我们必须引进这项技术。”厂总工艺师张铁军说。
仅半年时间,军工行业“首个”电弧增材制造平台就落地239厂,他们完成了从可行性论证到设备集成安装调试的全过程。
时刻准备着,型号应用从无到有
周六的上午,窗外阳光明媚,室内气氛凝固。
“还有40天就要总装完成,舱段尺寸发生变化,各位主任师都有啥好办法?”空气凝固了足足一刻钟,大家都觉得周期短,根本无法实现。孙主任说道:“铸造实在不行,模具设计及制造就得这么长时间了。”“挤压也是无能为力啊,咱厂不有电弧增材嘛。”“现在的确有一定的技术基础,但时间这么紧,我们不敢打包票啊。”“现在正是你们大展身手的时候,半个月完成2个舱段毛坯件制造,必须成功。”技术部韩维群主任郑重地给电弧增材团队下达了任务令。
这项紧急任务令着实让电弧增材团队有种泰山压顶的感觉,团队成员决定开启“13(小时/天)×6天”周工作模式。“内壁不加工(尺寸公差±0.5mm),这不容易啊,丝得由1.2换成0.8,再重新摸索工艺参数,”团队的步博士分析道,“实在不行,再微调工艺参数,慢慢逼近。”他们为精度要求奋战了几个昼夜,仍在不到1周时间内完成了2个舱段壳体毛坯件的电弧增材制造,最终在15天内成功完成了毛坯制造、检验及机加的全部工作。
院级专家验收评审的当天,团队成员在室外来回的踱步。得知舱段工艺攻关顺利通过,他们紧绷的脸上露出了轻松的微笑,主管技术的副总经理姚为也激动不已,“从无到有,零的突破,这次的成功虽然只是一件产品,但我们掌握了该技术的核心,就能推广应用在其他材料及型号产品上,这对于我厂乃至整个集团公司先进制造水平的提升可是个大喜事啊!但我们仍要不忘初心,智造未来。”
攻坚克难不止步,工艺软件齐开花
一次成功并没有让团队沾沾自喜,他们不忘初心,继续前行。
电弧增材制造铝合金的力学性能始终上不来,究其原因,主要是气孔。关于电弧增材铝合金的文献资料少之又少,基本获取不到任何有用信息。“电弧增材的基础是焊接,我们可以借鉴消除铝合金焊接气孔的技术手段,在焊接铝合金中消除气孔的方法主要是摆动,我们可以尝试着让机械臂摆动啊。”这句话点通了大家的思维,时针指向着9。“大家都回去吧,休息好了明天接着干啊。”
2年时间,他们成功突破了铝合金成形工艺和电弧增材自动控制软件这两大难题,实现了从三维模型到产品毛坯件的直接自动化制造,自主研发的软件将复杂结构件的编程工作量由原来的数天缩短至几分钟,成熟的工艺更是让制造的产品个个合格,大大缩短了整个研制生产周期,也进一步提升了电弧增材制造毛坯件的合格率。
电弧增材制造团队集智攻关的同时,不忘知识的传承,成功发表学术论文3篇、申报发明专利7项和软件著作权1项。
239厂将以科工集团公司“五个新一代”、“四项基础性支撑技术”和“三创新”为顶层牵引,加快催生自主创新与协同创新相结合的技术创新新动能,并以此次工艺创新为起点,继续深入开展更多新工艺技术的研发与推广应用工作,进一步提升我国航空航天等国防行业技术实力,进一步巩固我国世界大国的国际地位,为早日实现富强民主文明和谐美丽的社会主义现代化强国的“百年”目标添砖加瓦。